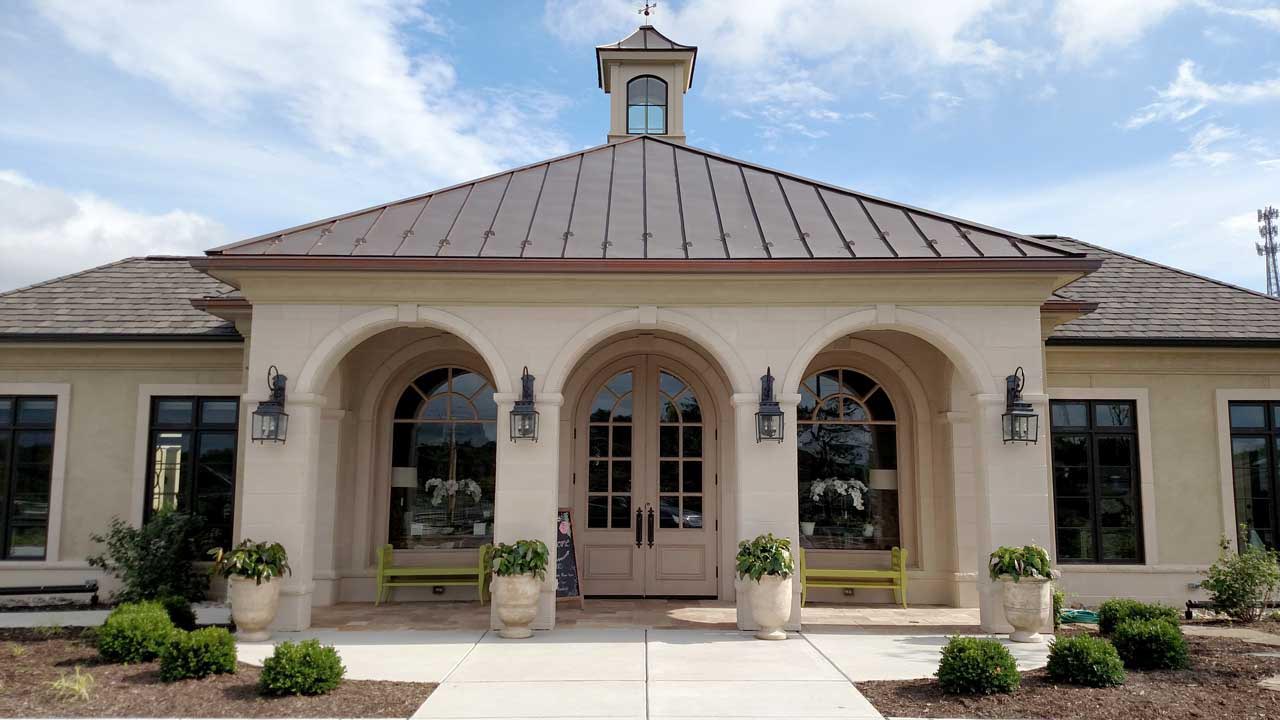
Architectural cast stone is a concrete masonry product that came into being around the 12th century A.D. in France, and is designed to simulate the appearance, texture, and aesthetic quality of limestone or other natural stones.
Today, architectural cast stone is manufactured at a lower cost and with better strength and durability than natural stone. Cast stone is typically used as an ornamental feature to accentuate the natural beauty of a masonry building, or as a compliment to other building materials.
Cast stone is typically made using the vibrant dry-tamp method, in which the cement and fine aggregate are compacted against the face of the mold using pneumatic pressure. The pieces are then finished and cured at high heat and humidity.
The result is an extremely strong cement matrix, which typically achieves a compressive strength of at least 6500 PSI when tested per ASTM C 1194, with a water absorption rate less than 6%. Compressive strengths over 10,000 PSI are not uncommon for well-tamped cast stone.
2501 West Lexington Street
Baltimore, MD 21223-1439
President and Owner